Cavitation measurement technique, project KonKav
Research of the correlation of cavitation effects and erosion in consideration of water qualities and wake (KonKav) is a joint research project of the BMWI. It investigates the influence of water quality on the cavitation of propellers. The aim is to develop a forecasting method to predict cavitation appearances at propellers. The first phase of the project KonKav I was launched in 2009, the second phase KonKav II in 2011.
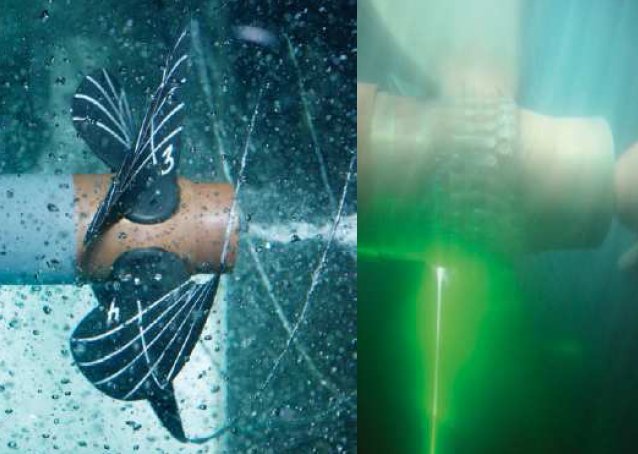
Within a subproject of KonKav I the Institute of General Electrical Engineering develops laser-optic measurement systems and applies them to determine in-situ the current velocity and concentration of air bubbles and solid particles in cavitation tunnels for the propeller inflow. Challenges are the distinction of particle kind and particle form in the flow, the quantitative determination of concentration, the determination of particle size, as well as the limited optical access in the cavitation tunnels. Furthermore, the cavitation phenomena at and behind the propeller are quantitatively characterized via several imaging technologies.
The measuring systems are tested in cavitation tunnels of the University of Rostock and the TU Berlin, in order to be employed in the cavitation tunnels of project partners Hamburgische Schiffbau-Versuchsanstalt (Hamburg Ship Model Basin) and Schiffbau-Versuchsanstalt Potsdam (Ship Model Basin Potsdam). The results serve as input and validation data for the development of a numeric forecasting method at the fourth partner, the Institute of Fluid Dynamics and Ship Theory at the Hamburg University of Technology (TUHH).
In KonKav II the data and numeric calculations collected at the models should be compared to measuring and simulation data of a real propeller. The aim is to consider scale effects in ship model basins (experimental) and simulations (numeric). For this purpose, the Institute of General Electrical Engineering equips a ship with optical measurement technique, in order to record the inflow to the propeller as well as the bubble size at sea. The researchers use an adapted PIV system with laser calibration and the IPI technique (Interferometric Particle Imaging) for bubble size determination. Challenges are the large working distance of 10 m maximum, the optical accessibility through windows in the ship’s fuselage, the related optical interfaces and changes of the refractive index in the beam path, as well as the adverse conditions on site.
Research group cavitation measurement technique
KonKav II:
- Dr.-Ing. André Kleinwächter
- Dr.-Ing. Eric Ebert
- Dipl.-Ing. Robert Kostbade
KonKav I:
- Dr.-Ing. Wilfried Kröger
- Dr. Stefan Borchert
- Dipl.-Ing. Stephan Höhne